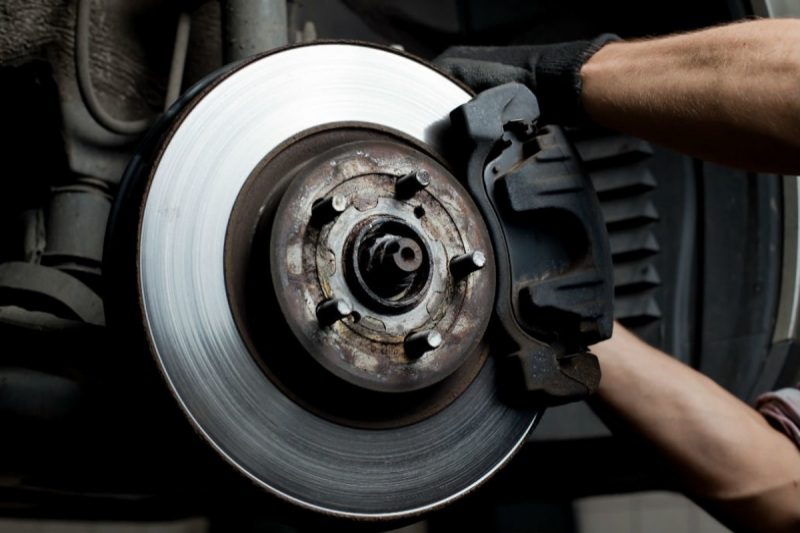
When it comes to ensuring your safety on the road, brake pads are a critical component that often goes overlooked.
You want your car to go fast, but it’s just as important that it can stop effectively. That’s where ceramic brake pads come in.
1. How do automotive braking components work?
When you step on the brake pedal, the master cylinder builds up pressure in the brake fluid lines.
This pressure is transmitted through the brake fluid to the pistons in the caliper.
The pressurized pistons then push the brake pads against the brake rotor or drum, creating friction that slows down the wheel’s rotation and brings your vehicle to a stop.
A brake pad consists of several key parts:
- Metal backing plate
- Thermal insulation layer
- Friction block.
The metal backing plate helps reduce noise and vibration, while the insulation layer prevents the intense heat generated during braking from transferring to the brake fluid, which could cause it to boil and form bubbles that impair braking performance.
The friction block, made of friction materials and binders, is responsible for creating friction against the brake rotor.
2. Common types of brake pads
A. Organic brake pads
Currently, organic brake pads, also known as NAO (Non-Asbestos Organic) pads, typically contain 10%-30% metal content, along with plant fibers, glass fibers, carbon, rubber, and other materials.
Thanks to years of development and material improvements, organic brake pads offer good wear resistance and noise control, making them suitable for everyday driving.
They also produce less dust and cause less damage to the brake rotors. However, due to material costs, organic pads tend to be slightly more expensive and are usually found on mid-to-high-end vehicles from the factory.
B. Semi-metallic brake pads
As the name suggests, semi-metallic brake pads use friction materials that consist of approximately 30%-65% metal content, including copper, iron, and other metals.
The main advantages of semi-metallic pads are their quick heat dissipation and excellent high-temperature performance, along with a relatively lower price point.
However, due to their metallic composition, they tend to be noisier during braking and cause more wear on the brake rotors.
Semi-metallic pads are commonly used in two main applications:
- As original equipment on lower-end vehicle models, where cost is a primary consideration
- In the aftermarket brake pad market for high-performance vehicles or racing applications, where their superior high-temperature performance is a key benefit.
C. Ceramic brake pads
Ceramic brake pads offer a solution to the shortcomings of both organic and semi-metallic pads.
They are primarily composed of a combination of mineral fibers, aramid fibers, and ceramic fibers. Because they contain no metallic content, ceramic pads significantly reduce noise when rubbing against the brake rotor. They also cause noticeably less damage to the rotor surface during the friction process.
Moreover, ceramic brake pads maintain a stable friction coefficient even at high temperatures. This feature avoids the brake fade that can occur with organic or semi-metallic pads due to material melting during prolonged or high-speed braking. This greatly enhances safety. Ceramic pads are also more wear-resistant.
3. Ceramic or semi-metallic: which are better?
The advantage of semi-metallic brake pads lies in their strong braking power and high-temperature resistance.
They can handle brake temperatures above 600°C or even 1000°C. However, their drawbacks are also clear: they produce more dust and are prone to brake squeal.
As a result, most ordinary passenger cars, especially those with engines under 2.0 liters, generally don’t use semi-metallic pads because owners find them aesthetically unappealing.
That’s why ceramic brake pads are now widely used in vehicles. Although their braking power may not match that of semi-metallic pads, they are sufficient for vehicles with engines under 2.0 liters.
Ceramic pads offer quiet operation, minimal dust production, and an attractive appearance. They also reduce pressure on the brake rotors, resulting in a longer service life.
Advantages of ceramic brake pads:
- Long lifespan, often exceeding 100,000 kilometers
- Wear-resistant and thermally stable at high temperatures
- Rapid heat dissipation and higher friction coefficient
- Excellent mechanical strength and physical properties, able to withstand significant pressure and shear forces